THIS IS HOW BRITISH MANUFACTURING COMPANY BAE SYSTEMS IMPROVED THEIR PRODUCTION SPEED
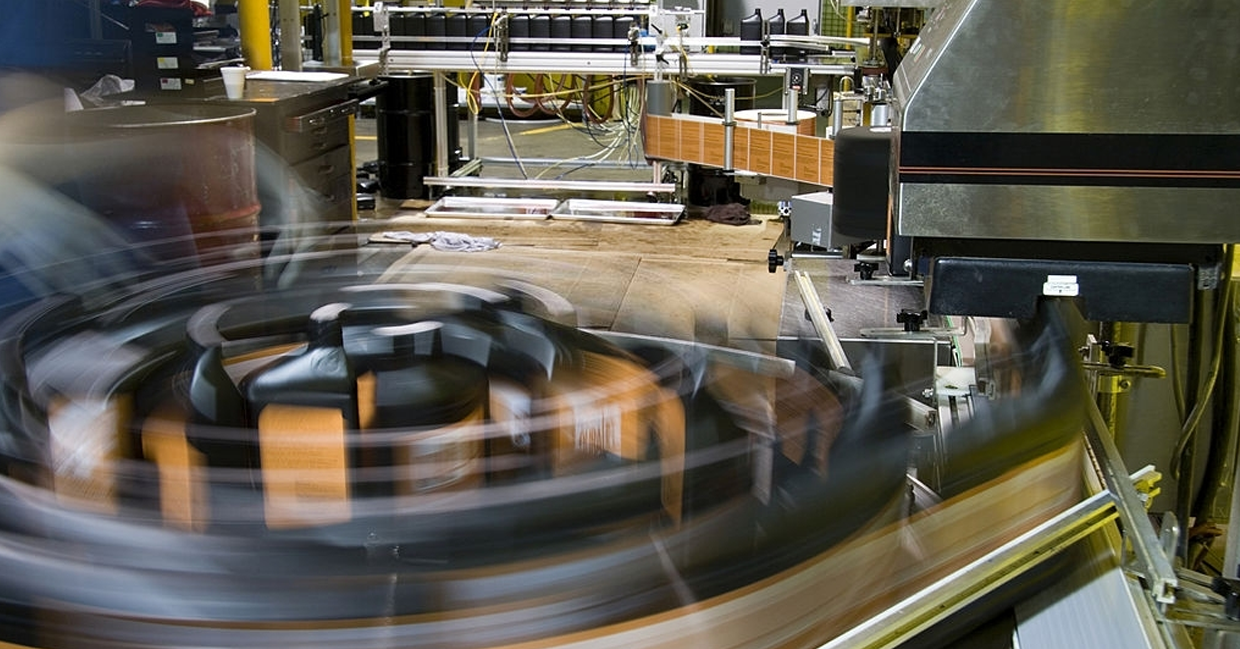
- 11/03/22
- GRAPES
Overview:
BAE Systems is a well-known British multinational defence, security, and aerospace company with over 85,800 employees and operations all over the world. They are one of Europe's leading defence contractors, as well as a major supplier to the US Department of Defense, as well as the militaries of Australia, India, and Saudi Arabia.
As a high-tech manufacturing plant, its central challenge was to consistently assemble complicated batteries. They had to face an immediate need to find new technologies and techniques to accelerate manufacturing production processes in response to increased customer demands.
The major goal was to replace existing manual processes with an automated Radio Frequency Identification (RFID) system to track and manage inventories, assets/tools, and workflow processes more efficiently. This would contribute to the company's overall goals of improving factory tracking and awareness, supporting ramped-up production initiatives, and decreasing non-value-added tasks.
The company sought to have a near-real-time view of its assets and processes and to combine that data with its existing sensor technology and ERP systems. It also desired that the solution be flexible and scalable enough to keep up with technological improvements and increasing corporate needs. The organisation lacked asset visibility and accountability in the lack of automation. As an extra complication, specific tools had to be manually tuned to meet compliance and regulatory standards.
APPROACH
Tapestry Solutions set out to provide an Internet of Things (IoT) solution for BAE Systems, employing RFID as well as Enterprise Sensor Integration (ESI) technologies that it has deployed across 50 Boeing factories.
ESI is a software solution that links a wide range of sensors and data sources to a single platform. ESI can be integrated with an organization's legacy RFID and sensor systems – independent of hardware or sensor type – as a sensor-agnostic solution. It connects sensor data to customer corporate systems like ERPs to improve operational automation and efficiencies. ESI can run in the cloud or on on-premises systems.
Boeing saved $100 million in the first year alone owing to reduced assembly time, automated asset collection and payment, improved inventory management, and increased quality and safety.
RESULT
The ESI-enabled RFID system has dramatically improved production capability at its factories all through its supply chain, improving current and future production plans for its customers. BAE Systems can now track 200,000+ assets, 30,000 parts, and an estimated 6,500 work orders at its sites, thanks to the system.
Recent Post
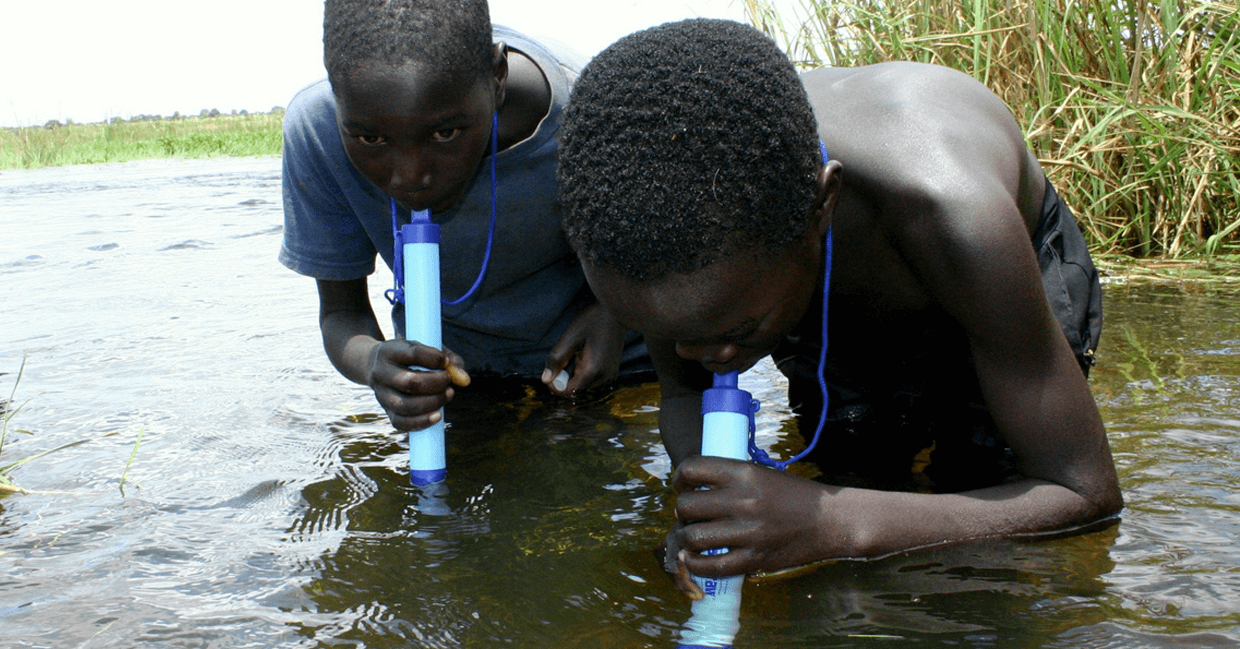
HOW TECHNOLOGY HELPED GHANA TO GET CLEAN WATER
- 24/11/22
- GRAPES
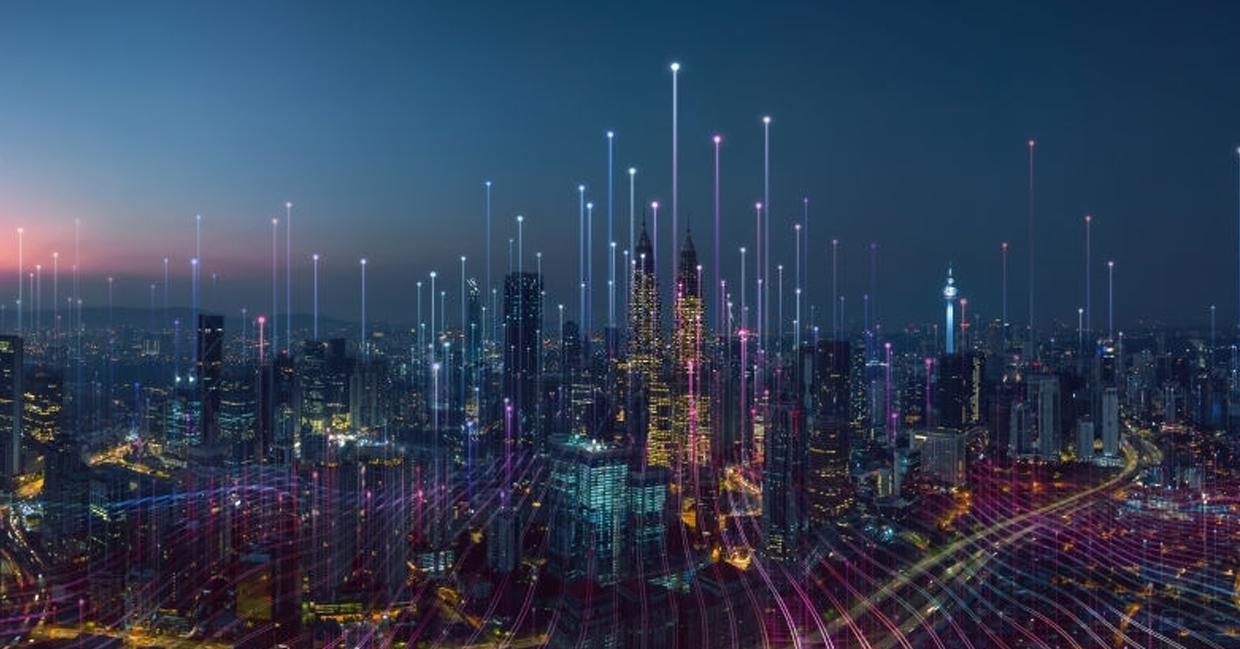
HOW THEY ARE TRYING TO BUILD THE HAPPIEST CITY ON THE EARTH
- 11/03/22
- GRAPES
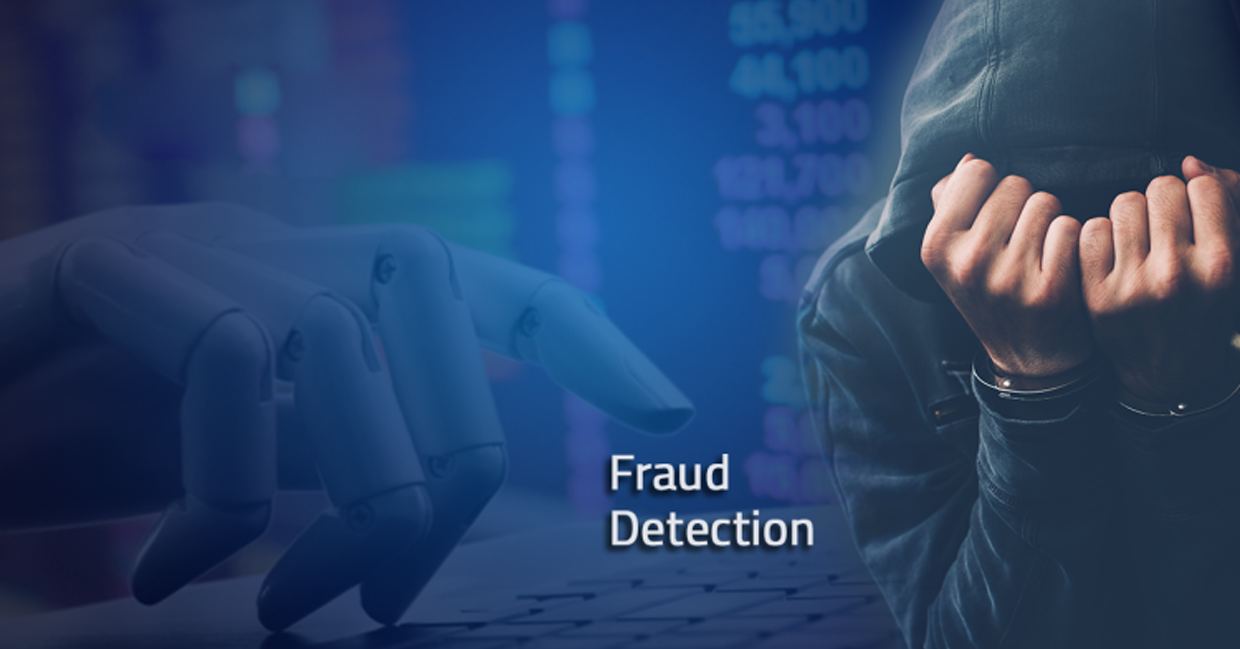
HOW THIS GLOBAL BANK USED AI/ML SOLUTIONS TO DETECT CHECK FRAUD
- 13/12/21
- GRAPES
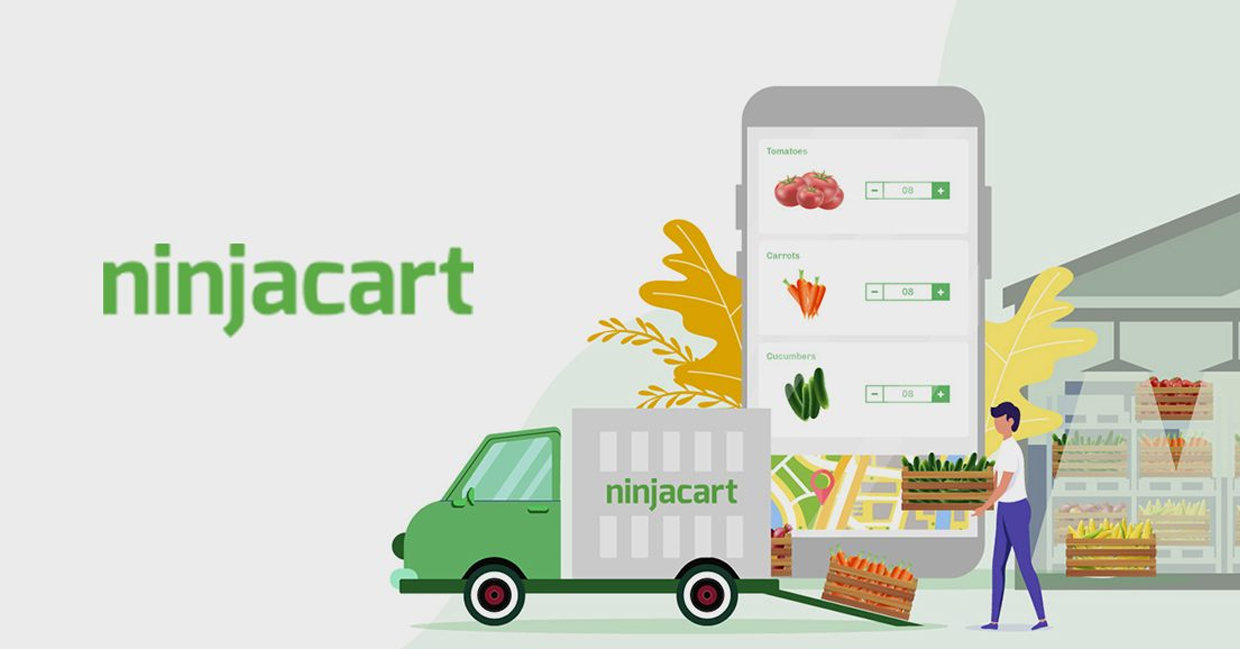
HOW NINJAKART IS IMPLEMENTING TECHNOLOGY TO BENEFIT FARMERS
- 13/12/21
- GRAPES
Copyright © 2021-2024 GRAPES (Global Resource for Automation Projects & Enterprise Services) Privacy Policy | Terms & Conditions | Disclaimer